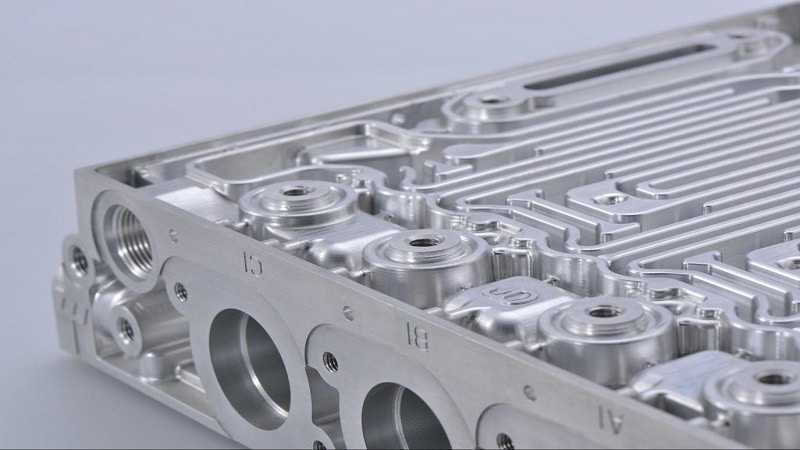
The world of manufacturing has witnessed significant advancements thanks to computer numerical control (CNC) machine tools.
These machines, which range from lathes to milling machines, utilize precise computer commands to craft intricate parts with high repeatability. At the heart of these CNC machines' accuracy and efficiency are servo drives such as Rexroth Indramat DKR Servo Drives.
This article will delve into the close relationship between servo drives and CNC machine tools and explain how they work together to create incredible products.
What is a Servo Drive?
A servo drive, also known as a servo amplifier, is an advanced electronic device that controls and regulates the performance of an electric servo motor. It operates by interpreting command signals sent from a controller, such as a computer or programmable logic controller (PLC), and subsequently modulating the motor current to achieve the desired movement or position.
Integral to its operation is a feedback system, often sourced from devices like encoders or resolvers, which monitors the motor's actual position and speed. By comparing this feedback to the command signal, the servo drive can make real-time adjustments, ensuring that the motor behaves precisely as intended. This precision control makes servo drives indispensable in applications like CNC machinery that require exact motion.
How Do Servo Drives Work With CNC Machines?
Precision Motion Control: At the core of a CNC machine is the need for exactitude. Whether it is a milling operation or a laser-cutting task, the machine must move its tools to the exact positions specified by the user or software. This requires motors to accelerate, decelerate, or change direction rapidly. Servo drives can manage these complex motions by adjusting power delivery to the motors, ensuring smooth transitions and accurate final positions.
Real-Time Feedback: The continuous communication between the servo drive and the CNC system is paramount. Through encoders or similar feedback devices, the servo drive receives real-time updates on the motor's current position. This dynamic feedback loop ensures the motor's movement aligns perfectly with the command signals, correcting any deviations immediately.
Synchronized Operations: Some CNC operations involve the simultaneous movement of multiple axes. In such cases, multiple servo drives work in tandem, ensuring all axes are perfectly synchronized. This synchronicity ensures the final product or machined part is of the highest quality.
Enhanced Efficiency and Productivity: Beyond precision, servo drives contribute to the efficiency of CNC machines. By optimizing power usage based on the task, they ensure minimal energy wastage. Additionally, with the ability to execute tasks quickly and accurately, they contribute to higher productivity levels in manufacturing settings.
Safety and Protection: Advanced servo drives come equipped with safety protocols that can detect issues like overcurrent, overheating, or motor stalls. In the event of a potential problem, the servo drive can take preventive measures, like decelerating the drive or shutting down the motor, to protect both the machine and the operator.
Flexibility and Adaptability: Modern CNC machines often come with features that allow for the easy addition or removal of components, tools, or fixtures. Servo drives can adapt to changing applications through the use of various plug-in cards and corresponding software modules that are easily inserted into the basic unit.
Rexroth Indramat DKR Servo Drives
Although the Indramat DKR series of servo drives is now considered a legacy product, it is essential to recognize that the DKR series was ahead of its time in many respects. Today, the DKR series is still a crucial component in many CNC projects around the world. Here is why:
Dynamic Performance: Known for its rapid response times, the DKR series is well-suited for applications that require high-speed operations with quick changes in acceleration or deceleration. The drives can be configured to divide a single motor revolution into as many as 4,000,000 parts, an impressive testament to its precision!
Multiple Feedback Systems: The DKR series was designed to be compatible with motor feedback or several different external feedback systems. This flexibility ensures that it can cater to a broad range of applications with varying precision needs.
Integration with Indramat Motors: The DKR drives are optimized for use with Indramat's 2AD series motors or 1MB frameless motors, ensuring seamless compatibility and maximum performance.
Modular Design: The DKR series offers a modular design that allows users to select components based on their specific needs. This makes it easier to customize solutions based on the application's requirements.
Built for Harsh Environments: Designed with durability in mind, the DKR drives can operate reliably in demanding industrial settings. They are built to resist the wear and tear commonly seen in such environments.
Safety Features: The DKR series comes equipped with several safety features to ensure reliable operation. These safety functionalities ensure that the drive and motor operate within safe parameters, reducing the risk of damage or accidents.
Legacy and Support: Even as newer models and technologies emerged, many industries continue to rely on the reliability and performance of the DKR series. As a result, there remains a notable demand for supply and support services specific to the DKR series.
Conclusion
Servo drives are an integral component of CNC machines, ensuring they operate with the highest precision, efficiency, and safety. From legacy products like Rexroth Indramat DKR servo drives to the state-of-the-art advancements of today, the synergy between servo drives and CNC machines will drive greater achievements in manufacturing and production.