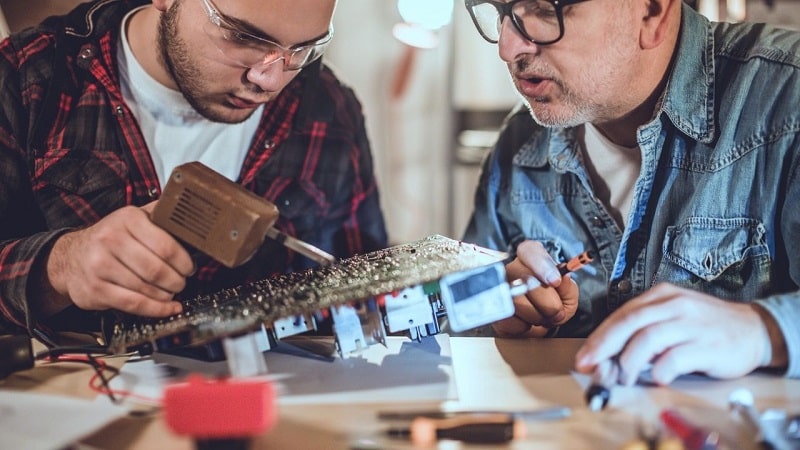
A lot of advancements have taken place in the electronics industry ensuring that the least mistakes are done. But no matter how perfect you create something and one or the two mistakes are bound to occur.
There are many certification courses and training modules that are specifically focused on minimizing the errors in the electronic industry. Yet you can not escape them. The real challenge is to address them as they come up from time to time.
To address any error, you need to be privy to the errors that make you capable enough to address them. A deep understanding of the errors will help you to quickly eliminate them.
Hence, production schedules can be maintained and the possibility of future errors can be eliminated.
Below is the list of five common errors and how to resolve them
1. Disturbed joint
When an alloy is solidified and there is movement that occurs that can result in a disturbed joint. The distubed joint becomes hard and rough. On the joint surface, you will see a ripple pattern which is indicative of the error. However, if we look at the primary cause of the error, it is the movement occurring in them. The reasons for the movement can be mechanical, human or both.
To resolve those errors, you have to reheat joints and let it cool it properly. If you want to stop the error, make an effort and find out the sources of the vibration and make sure that proper stabilization methods are taken while soldering.
2. Solder-starved Joint
A solder starved-joint does not have enough solder, even if you make the required electrical connection, less solder weakens the joint and increases the possibility of the failure and errors. You have to make sure that there is enough solder to prevent error.
If you want to resolve this error and ensure the long term stability, you have to reheat the joints and use more solder till the joint is made strong.
3. Untrimmed leads
Untrimmed leads have a high length that is the reason errors occur as lengthy leads have the risk of coming into contact with other leads that can lead to the unexpected short circuit. Even when one lead remains uncut, the possibility of it coming into the other traces is high and they should be avoided.
All you have to do is to cut all the unnecessary lengths of the lead and make sure that this process is followed from time to time.
4. Cold solder joint
If solder does not melt properly, chances are that cold solder joint is likely to occur because of lack of heat. Cold solder joints are rigid, rough and strange in appearance. This solder error weakens the joint, making it susceptible to failure. They can cause errors at any point of time, or they can crack any time.
5. Solder bridge
When you apply the excessive solder, then also a solder bridge is likely to occur in the separate joints melting together. This activity creates the possibility of unplanned connection, creating an impact on the overall function of the board.
All you have to do to deal with this error is to remove the unnecessary solder between the joints with a hot iron tip or solder wick. To eliminate this error, you have to measure the amount of solder that you have to use so that it can create an acceptable joint and excess alloy can make the bridging and other errors.
You need to test them alot to see what is the sufficient amount of the alloy. With testing, you can easily find out.
Well you can avoid these recurring errors, all you have to do is to get your people trained well with well certified courses in the required field. This training will help them to identify the error at the early stage thereby helping them to prevent the errors occuring in future.